Understanding AQL Standards in Quality Control for Overseas Manufacturing
When working with overseas manufacturers, quality control (QC) is a critical part of ensuring the product meets the required standards before it is shipped to its final destination. One of the most common tools used in quality control is the AQL (Acceptable Quality Limit) standard. Understanding how AQL works and how it applies to quality control in overseas manufacturing can help businesses minimize defects, maintain brand reputation, and reduce costs associated with product returns or rework.
10/7/20244 min read
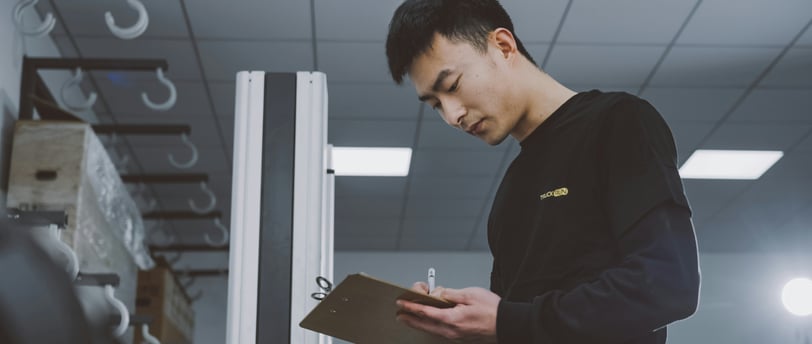
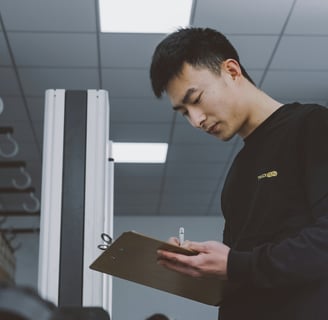
What is AQL?
AQL stands for Acceptable Quality Limit or Acceptable Quality Level, a widely used standard for determining the maximum number of defective items that can be considered acceptable during the sampling of an inspection lot. It’s a statistical tool that helps businesses and manufacturers decide when a production batch is of satisfactory quality or when it falls below standard and requires action, such as a rework or rejection.
The AQL is commonly used in industries like consumer electronics, textiles, toys, and furniture, especially when working with overseas manufacturers where continuous production monitoring may not be feasible due to distance.
The Basics of AQL Sampling
AQL is a statistical sampling method that works by inspecting a random sample of items from a production lot. Instead of inspecting every item in a large batch (which is often impractical), manufacturers inspect a specific quantity, using the results to determine the overall quality of the batch. The AQL level is expressed as a ratio or percentage that reflects the number of defects that are allowed before a batch is rejected.
For example, an AQL of 1.0 means that, for every 100 items inspected, a maximum of 1 defective item is acceptable. If there are more than 1 defective item, the batch may be rejected or require corrective action.
Key Terms in AQL
To better understand how AQL works, let’s define some key terms:
Lot Size: The total number of units produced in a batch.
Sample Size: The number of units that will be inspected from the lot.
Acceptance Number: The maximum number of defective units allowed in the sample for the batch to be accepted.
Rejection Number: If defects exceed this number, the entire lot is rejected or subject to corrective actions.
AQL Levels and Categories of Defects
Defects are typically categorized into three levels of severity:
Critical Defects: These are defects that could be dangerous to the user, violate regulations, or make the product completely unusable. These defects often have an AQL of 0, meaning any critical defect would result in rejection of the batch.
Major Defects: These are defects that might affect the function, performance, or appearance of the product and would likely lead to consumer dissatisfaction. An example might be a large scratch on a screen or a product that doesn’t work as intended. AQL levels for major defects are commonly set between 1.0 and 2.5.
Minor Defects: These are smaller, cosmetic issues that don’t affect the performance of the product but might affect its appearance. Consumers may still be willing to purchase the product, but a high level of minor defects can hurt brand reputation. AQL levels for minor defects are typically set between 2.5 and 4.0.
How AQL Is Used in Overseas Manufacturing
When outsourcing production to overseas manufacturers, businesses must ensure that products are of high quality before they are shipped. AQL standards provide a reliable method for assessing product quality without the need to inspect every item. Overseas manufacturers are usually required to follow these steps:
Determine the Lot Size: Before production, the business and manufacturer agree on the production batch size.
Choose the AQL Level: Depending on the product type and the acceptable risk level, businesses will set different AQL levels for critical, major, and minor defects. Products that require high reliability and safety (e.g., medical devices) will have much stricter AQL levels compared to, say, decorative items.
Conduct Inspection: A random sample from the batch is inspected, and the defects are categorized as critical, major, or minor.
Make Decisions Based on Results: If the number of defects falls below the acceptance number, the lot passes. If defects exceed the rejection number, the lot is rejected, and corrective actions are needed, which might include re-inspection, reworking defective items, or scrapping the entire batch.
Benefits of Using AQL in Quality Control
Cost-Effective: AQL allows manufacturers to inspect a representative sample rather than every single item, saving time and money.
Objective Standards: AQL provides clear and standardized thresholds for acceptable quality, removing subjective judgments during inspections.
Consistent Product Quality: By setting agreed-upon AQL levels with manufacturers, businesses can maintain consistent product quality and avoid unexpected issues.
Risk Management: AQL standards help businesses balance the need for high-quality products with the reality of manufacturing imperfections. A business can set stricter AQL levels for high-risk products and more lenient ones for lower-risk items.
Challenges of AQL in Overseas Manufacturing
While AQL offers many benefits, there are challenges when applying it in overseas manufacturing:
Communication Barriers: Miscommunication about acceptable quality levels and inspection procedures can occur, especially with language differences. Clear communication and proper documentation are essential.
Cultural Differences: Some manufacturers may have different interpretations of what constitutes a defect. Training and alignment on quality expectations are critical.
Quality Control Costs: The cost of hiring third-party inspectors or performing in-house inspections can add to the overall production cost. However, these expenses are often offset by the prevention of costly reworks or product recalls.
Logistics and Time Delays: If a batch fails the AQL inspection, reworking defective units or re-inspecting can delay shipment times, impacting the supply chain.
Conclusion
AQL standards are a vital component of quality control in overseas manufacturing. By using statistical sampling methods, businesses can manage the quality of their products in a cost-effective and efficient way. When used correctly, AQL inspections can significantly reduce the risk of defective products reaching customers, protect brand reputation, and improve relationships with overseas suppliers. However, to reap these benefits, businesses must clearly communicate AQL levels, ensure thorough inspections, and stay engaged with their manufacturing partners.
Contact Info
Subscribe
Email: info@cgtco-hk.com
Add.: Flat 24, 3/F, Block A, Hi-Tech Industrial Centre, 5-21 Pak Tin Par Street, Tsuen Wan, N.T., Hong Kong
Tel.: (852) 2498 1678
© 2024. All rights reserved.
Company
Stock